Process
OF PREPARATION
OF MOuLDED FIBRE

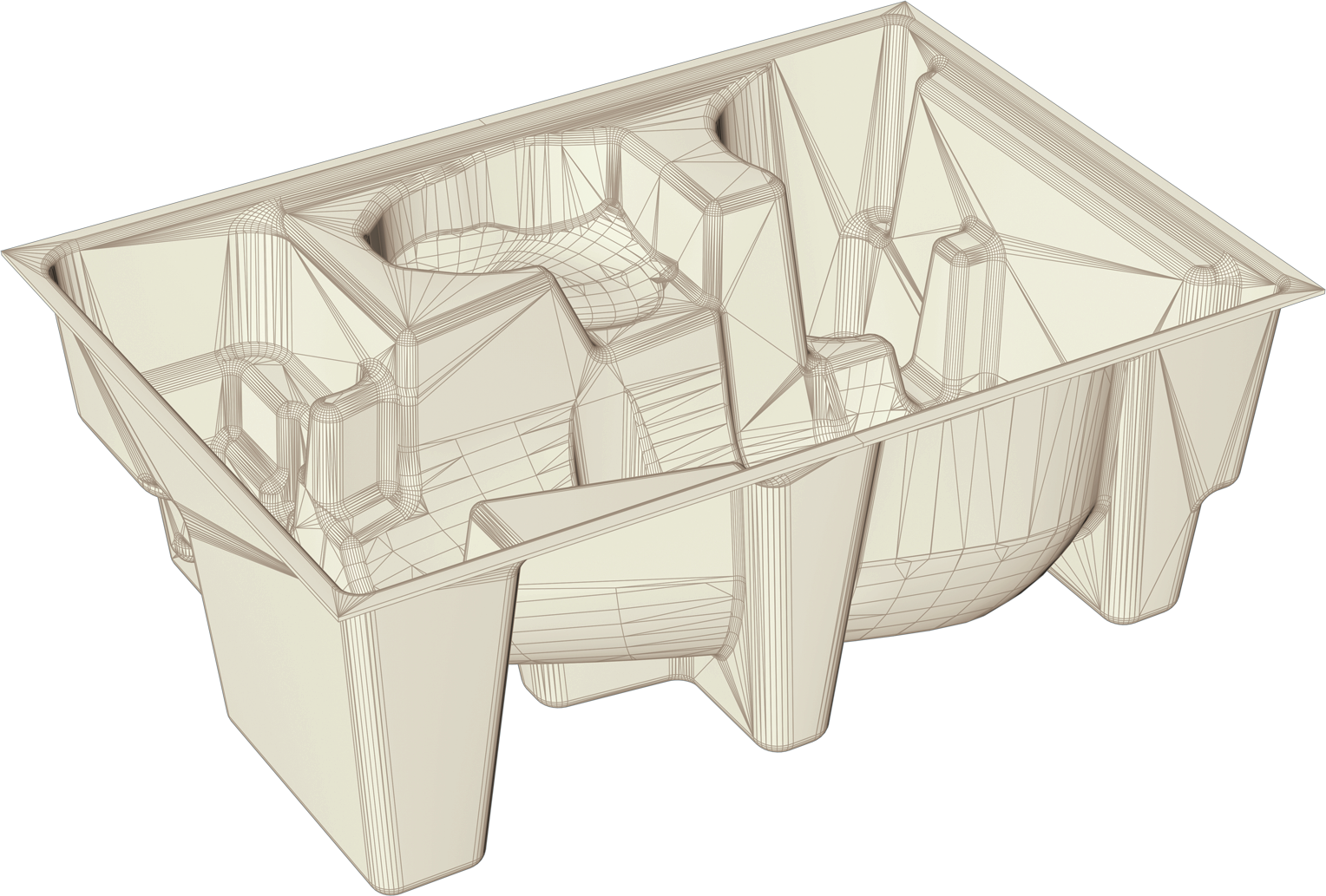
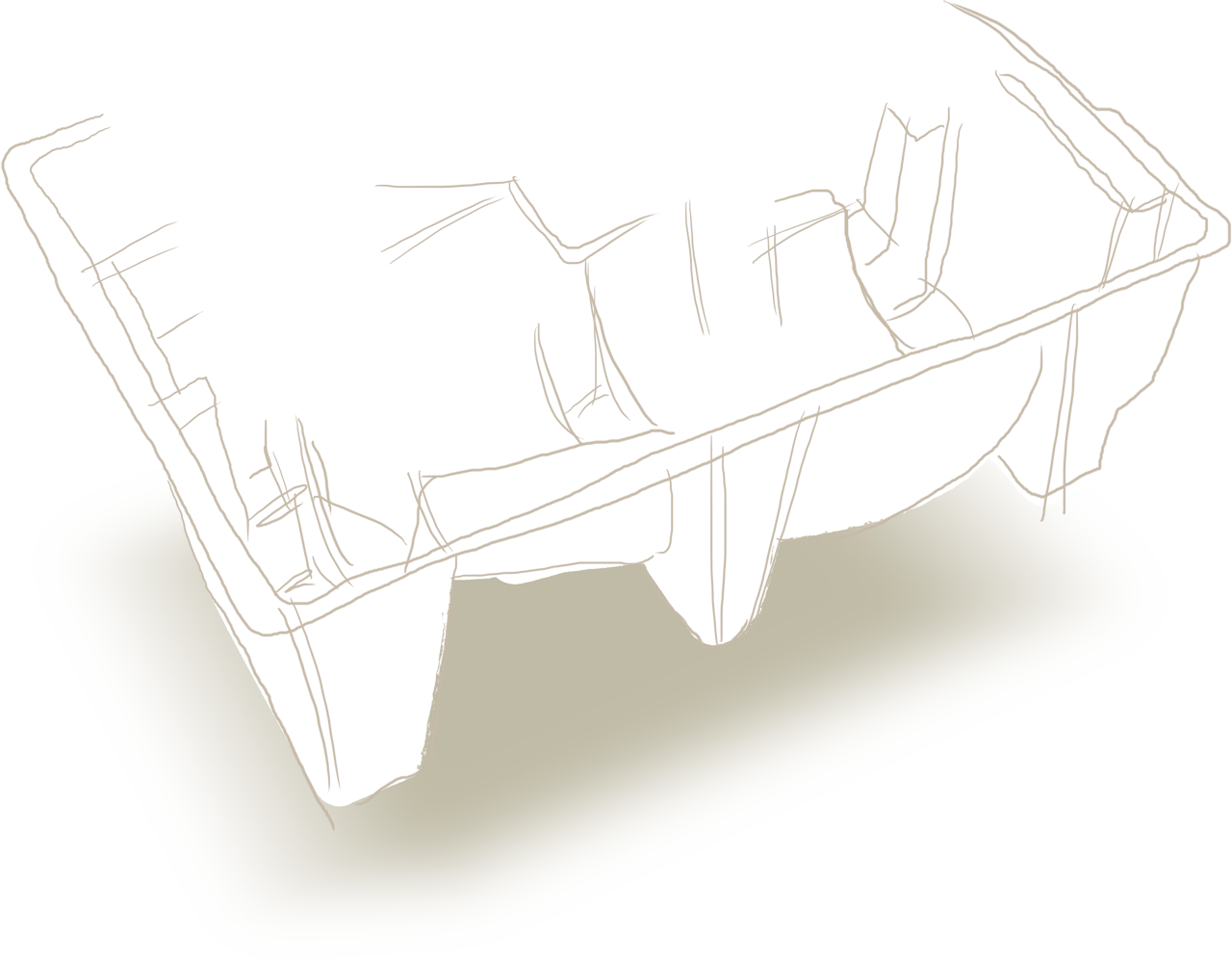
3. Final product
The final step of the preparatory process is the manufacture of a sample mould and subsequent manufacture of a real sample. Samples are used for the verification of real shapes and for the drop tests. Material used for the manufacture of the samples is of the quality identical with that for the standard production.
2. 3D design
The second preparatory step is the set-up of a full-size 3D model. For the set-up of the 3D model we need that the customer would provide us with real samples or models of the product to be packaged.
1. Concept
After all input data have been defined, a simple sketch of a tray is drawn. This serves to the initial price calculation and shows the basic packaging principle.
Production
MOULDED FIBRE PRODUCTION PROCESS
Conventional line
Collected waste paper (cardboard or newspapers) is precisely weighted and put into the hydropulper. Here paper is mixed with water and within 15 to 20 minutes it is de-fibred to establish pulp. This mixture is pumped through a two-stage filtration where, in the first cycle, heavy impurities (small stones, sand, paperclips) are separated and, in the second cycle, all light impurities are separated (wood, plastic, polystyrene, and adhesive tapes). Pure pulp is stored in tanks and ready forsubsequent use. The last step of the pulp preparation is its mixing to reach required operation parameters. The whole process is fully automatic.
The second production step is pumping of pulp into the forming line where it is sucked onto aluminium moulds. After residual water has been exhausted, the already finished product is transferred to a drying conveyor. The drying process is automatically monitored; during this process humidity, temperature, and volume of drying air is controlled. The product drying time ranges between 25 and 35 minutes, in relation to its size and thickness of material.
In the event a customer requires high surface quality or exact inside dimensions of a tray, products are after-pressed in a hot mould. The effect of a high temperature and of a multiple-ton press results in a smooth surface. To reach exact outside dimensions, product edges are trimmed, in relation to the size of a box. The waste from trimming is recycled for further production.
THERMOFORMING
Collected waste paper (cardboard or newspapers) is precisely weighted and put into the hydropulper. Here paper is mixed with water and within 15 to 20 minutes it is de-fibred to establish pulp. This mixture is pumped through a two-stage filtration where, in the first cycle, heavy impurities (small stones, sand, paperclips) are separated and, in the second cycle, all light impurities are separated (wood, plastic, polystyrene, and adhesive tapes). Pure pulp is stored in tanks and ready forsubsequent use. The last step of the pulp preparation is its mixing to reach required operation parameters. The whole process is fully automatic.
The second productions step is the pumping of pulp to the forming section of the line where it is sucked onto aluminium moulds. After residual water has been exhausted, the already finished product is transferred to hot forming moulds. During the drying process, still wet trays are pressed under high pressure. Temperature of the moulds is automatically controlled, varying between 100 and 220 °C. The product drying time varies between 60 and 150 seconds, in relation to the size and weight of the tray.
In the event a customer requires exact outside dimension, product edges are trimmed in relation to the size of a box. The waste from trimming is recycled for further production.